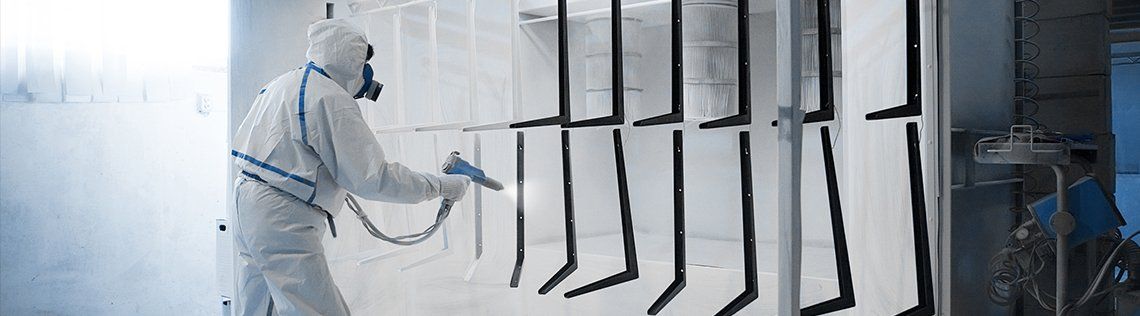
Powder Coating
Restore the finish on your products with powder coating services from Northwest Powder Solutions Inc.
With our large ovens, dip tanks, and fully-equipped facility we are able to handle any size project up to 23 feet in lengh.
. We only use powders from top powder manufacturers such as Tiger Drylac, Prismatic Powders, Cardinal Paint and many more.
What Can Be Powder Coated?
We are able to powder coat a variety of products and parts including:
- Metal fencing, railing, guard rails
- Industrial parts (aluminum or steel)
- ATV frames/parts
- 4x4/4wd bumpers, brush guards, grills, etc.
- Single engine airplane parts
- Furniture - garden chairs, benches
- Trade show fixtures and displays
- Grill guards
- Motorcycle wheels, frames, etc.
- Auto parts
- Bicycle
Northwest Powder Solutions Inc. provides powder coat options such as different textures and colors so you can choose the best finish for your product.
The Powder Coating Process
- Powder coating is a type of coating that is applied as a free-flowing, dry powder. The main difference between a conventional liquid paint and a powder coating is that the powder coating does not require a solvent to keep the binder and filler parts in a liquid suspension form. This makes it an eco-friendly alternative to conventional paint.
- The coating is typically applied electrostatically and is then cured under heat to allow it to flow and form a "skin." It is usually used to create a hard finish that is tougher than conventional paint. Before the powder coating can be applied, the metal must be cleaned. The removal of oil, soil, lubrication greases, metal oxides, welding scales, etc. is essential prior to the powder coating process. At Northwest Powder Solutions, we typically use a chemical bath process to remove these impurities.
- Chemical pre-treatments involve the use of phosphates or chromates in a submersion application. These occur in multiple states and consist of degreasing, etching, desmutting, various rinses and the final phosphating or chromating of substrate. The pre-treatment process cleans and improves bonding of the powder to the metal. Once themetal is cleaned, the application of the powder can begin.
- The most common way of applying the powder coating to metal objects is to spray the powder using an electrostatic gun (or Corona gun). The gun imparts a positive electric charge on the powder, which is then sprayed towards the grounded object by mechanical or compressed air spraying and then accelerated toward the piece by the powerful electrostatic charge.
- After the application, the object is then heated at approximately 400 degrees F. the powder melts into a uniform film and is then cooled to form a hard coating. It is also common to heat the metal first and spray the powder onto the hot substrate. Preheating can also help to achieve a more uniform and thicker finish.
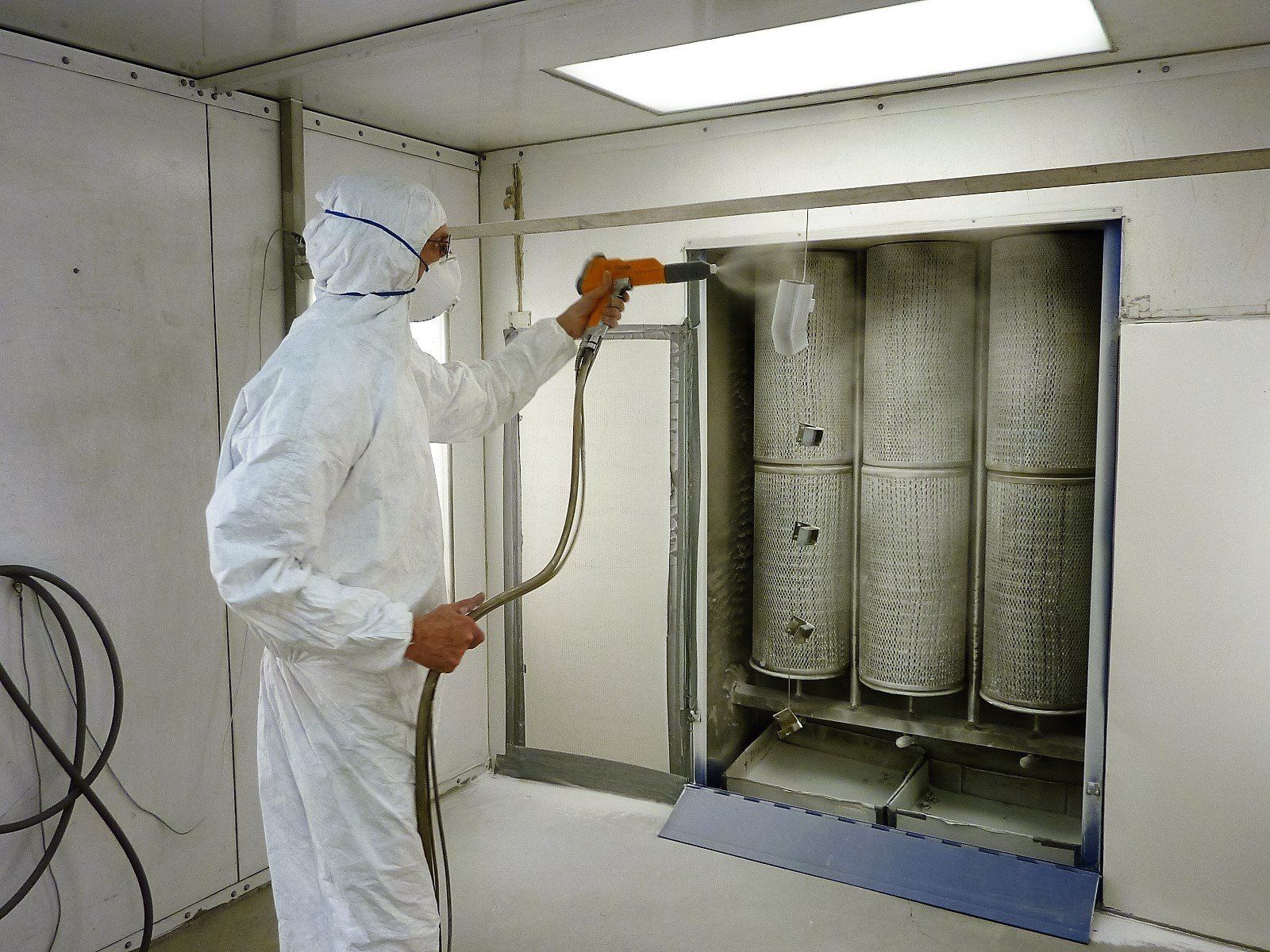
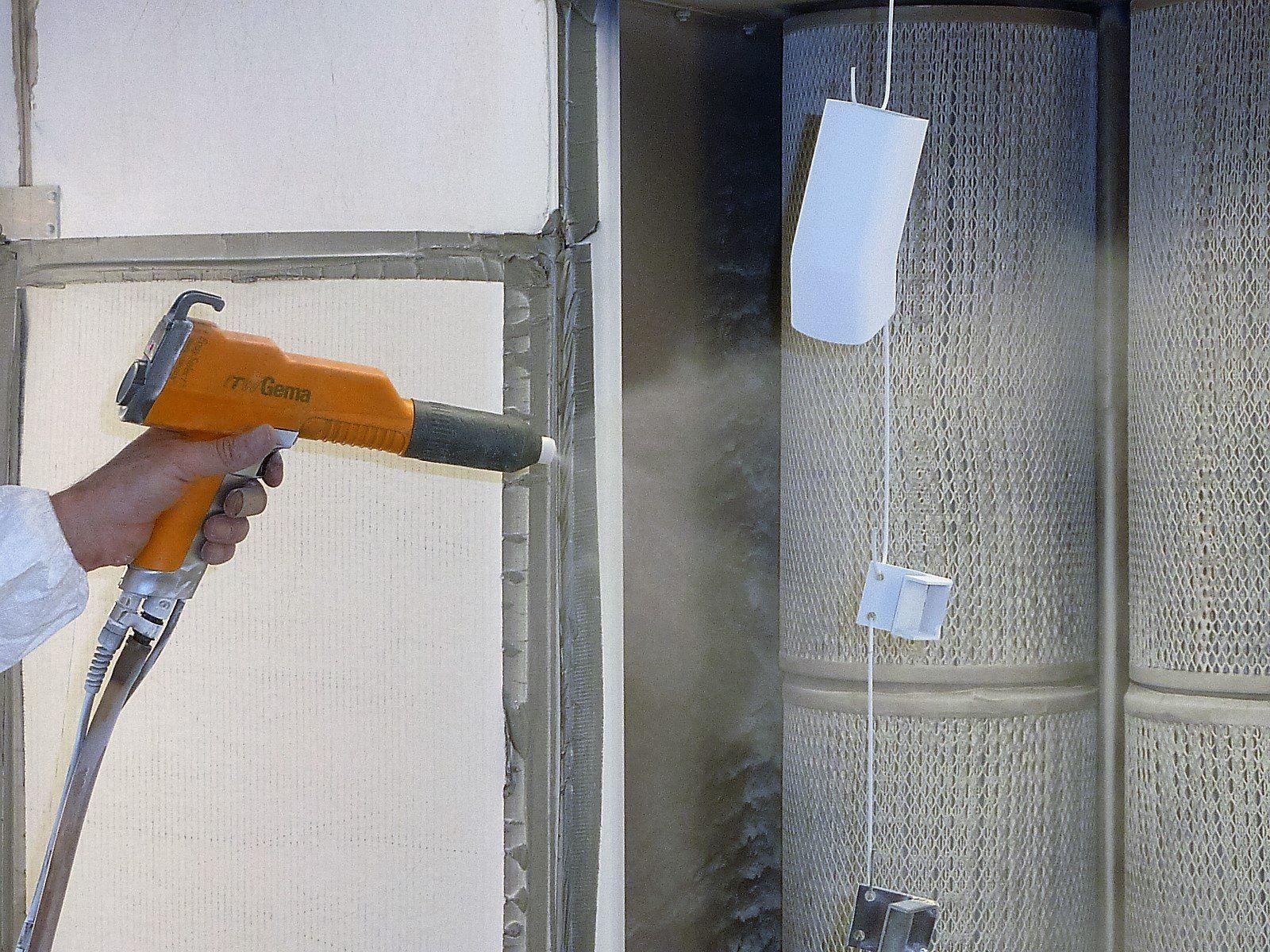
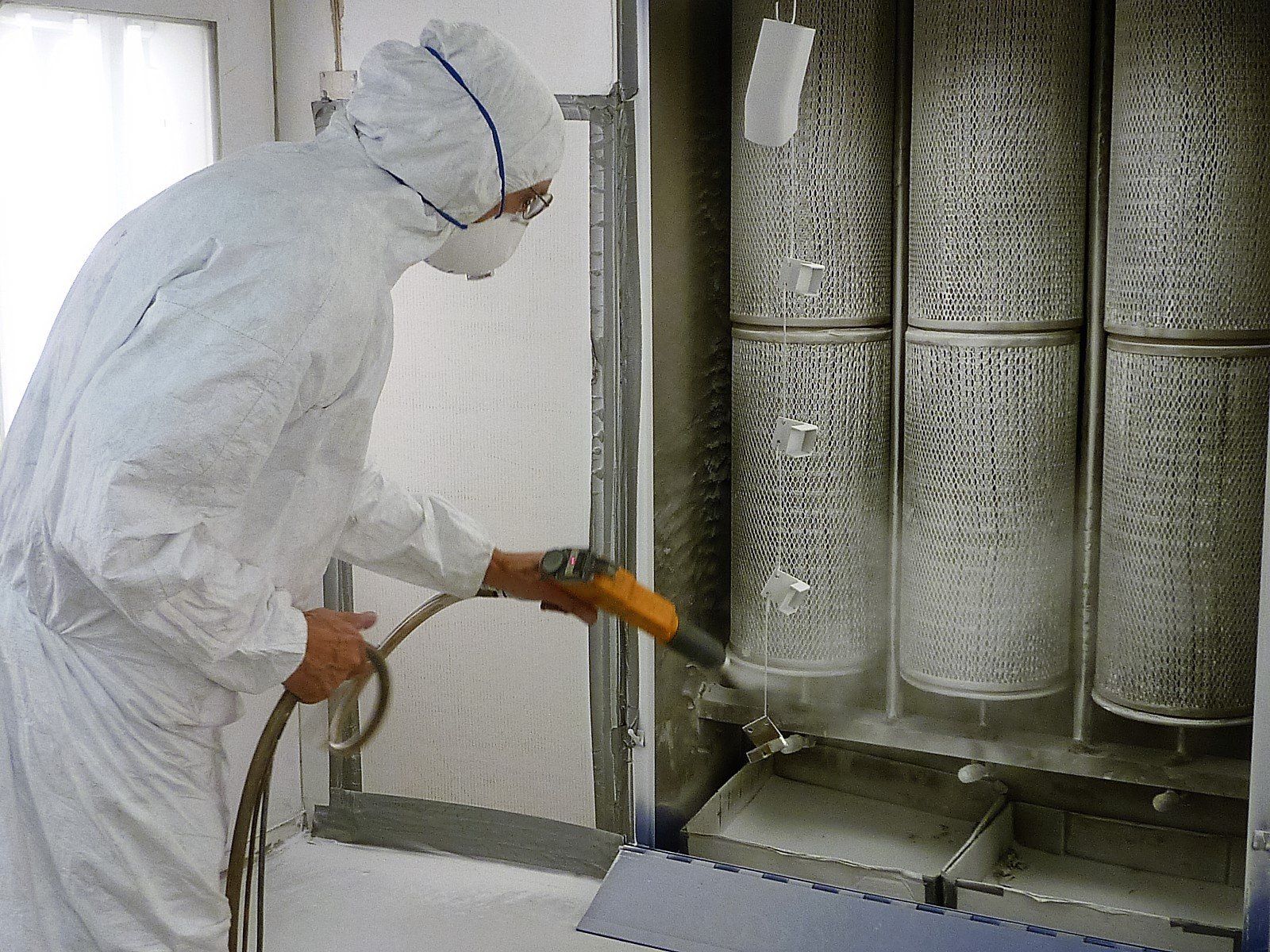
For more information about our powder coating process, call us at (253) 395-6282.